Custom Screen Printing is a complicated and (at least in the opinion of Shirt Art employees) fascinating process. It is both labor and machinery intensive. Properly done it requires a great attention to detail at every stage of the process to achieve a superior
Custom Printed T-Shirt. It also requires some specialized machinery, but of course the results are only as good as the knowledge, experience, and care given by the operator.
As you may know,
Screen Printing Pricing is very quantity dependent. This is because the Set-Up process to print 1 shirt or 1000 shirts is the same. So let's start there, with the Set-Up process for a 1 color T-Shirt print.
The Screen
The single most important tool used by Screen Printers is the Screen. As it's name implies, it is essentially like a piece of mesh with holes that allow the ink to pass through onto the T-Shirt, polo shirt, or other garment. Originally this mesh was made of silk, hence the name silk screening, but currently it is most often a high strength nylon. (For more on Screen Printing History,
click here) Aside from various subtleties such as type of material and type of weave, the basic characteristics of a screen are it's hole size and tension. At Shirt Art we predominately use high tension screens that we stretch ourselves, giving us more control in our print. As far as mesh size, we use a wide variety, among which the most frequently used sizes are 86 (holes per inch), 110, 156, 200, 230, 305, and 355. Essentially you can think of these mesh sizes as corresponding to resolution, for instance a 355 hole per inch screen would hold much more detail than an 86 hole per inch screen. So you might ask, "Why not only use the highest mesh screen, since that provides the most detail?" The answer is that we do use the highest appropriate mesh at all times, but there are practical limitations determined by the type of ink being used, and whether the print is going on a light or dark T-Shirt. A dark T-Shirt needs a thicker and more opaque ink to hold it's color, and these inks often are too thick to pass through the higher meshes. We do employ a number of techniques to combat this issue, of which an advanced technique called "Simulated Process Printing on Darks" is paramount. Using this technique we routinely use 230, 305, and even 355 mesh screens for our Custom Prints on dark T-Shirts.
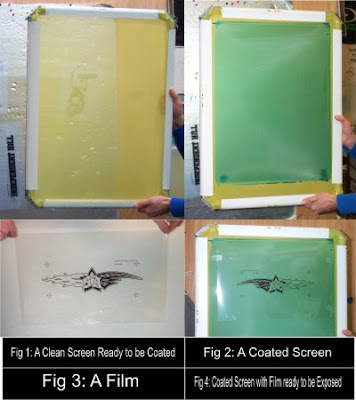
Reclaiming and Coating the Screen
So once the appropriate screen mesh has been selected, the screen must be cleaned of all past images and inks, and then left to dry (figure 1). Once it is completely dry, it must be coated with a light sensitive photo-emulsion. This substance comes shipped as a liquid. It is water soluble and has a consistency similar to that of ordinary paint. It is applied to each screen individually by hand using a scoop coater, which is essentially a long trough that allows a thin layer of the emulsion to coat both sides of the mesh. Once this process is complete the coated screens are left in a dark room until the photo-emulsion dries due to exposure to the air. At this point the screens are ready to be exposed to light(figure 2).
"Burning" The Screen
We now have a screen with a dry layer of photo-emulsion coating both sides of the mesh. We started with a screen that was entirely open mesh, and would allow ink to pass through at any point, and now we have a screen that is covered with dry photo-emulsion and will not let ink pass through anywhere. However in order to produce a
Custom Screen Print we must have something in between the two, namely a stencil that will allow the one color of ink in the screen to pass through the mesh and be deposited on the
Custom T-Shirt in only the areas we want the ink to be. This is where our in-house Artist comes into play. The artwork he creates on the computer is printed out in black ink on transparent film (figure 3). Each color of the artwork is first separated and then printed out by itself, because each screen can only print one color of ink. These films are then fixed to the screen (figure 4), at which point we use a Metal-Halide Bulb Exposure Unit to expose the light sensitive photo-emulsion to a light source. After the screen has been exposed (or "burned" in Screen Printing lingo) it is rinsed with a steady stream of water. Wherever the light was able to reach the photo-emulsion directly the photo-emulsion remains hardened, continuing to block up that portion of the mesh. However where the black ink of the computer film blocked the light from getting through the photo-emulsion washes away, leaving an open area for ink to pass through the mesh and creating our stencil.

Fig 5: Exposure Unit in Action

Fig 6: Screen Burned and Rinsed -- Stencil Complete
Tape it Up and Lock it Down
After the rinsing process is complete, and the stencil is opened up, the screen is allowed to dry once again. Then tape is used to cover the sides, top and bottom of the mesh area, where the scoop coater is unable to deposit any emulsion, so that no ink is able to slip through onto the shirt. The screen must also be examined for "pinholes," which are tiny holes in the emulsion that would let ink pass through to leave tiny unwanted spots of ink on the Custom T-Shirts. If any of these pinholes are present they must be covered with a small piece of tape. Similarly, during the print run a very close eye must be kept on each and every shirt to ensure that no more pinholes open up once the run has started. Once the Taping Up process is complete, the screen must be aligned in the printing press so that it is level with the board on which the Custom T-Shirts will be loaded, so that it is straight, and also centered, and then Locked Down into place. Then the ink must be placed into the screen, as well as a squeegee which draws the ink across the stencil and deposits it onto the shirt. In addition, if it is a multicolor print, each screen must be Registered to the others so that the various colors will line up correctly. A rough registration is accomplished during this Lock Down process. Then test prints must be done and adjustments made using the microregistration knobs of the press, which allow for tiny movements to be made to each screen, until all colors are in precisely the right spot relative to each other.

Production
And now we've finally reached the Printing stage. As you can see, there is quite a bit involved in setting up a
Custom Screen Print. Whether we're printing this image on 1 shirt or 1000 shirts, we still have to perform all of these steps before we are ready to print the first shirt. Once this has all been accomplished the printing process is fairly straight forward and can move at a relatively high speed. Each shirt must be loaded individually, with care taken to make sure it is put on the board straight, then the squeegee must be passed across the screen to push the ink through the entire stencil. In Fig. 8 you can see the Green Ink Screen set up and ready to print on our Automatic Press. If there is another color to be printed it is then ready to print, by spinning the board with the loaded
Custom T-Shirt over to the next screen. Then the shirt must be removed from the board and sent through the Dryer. The Dryer is exactly what it's name implies, essentially a conveyor belt that goes through a heated tunnel. The ink we use on the shirts is called Plastisol, and is essentially a liquid plastic that needs to be heated to roughly 330 degrees Fahrenheit in order to properly cure. Once this has been done, the
Custom T-Shirt has a layer of plastic on it, which should outlast the T-Shirt material. Fig. 9 shows the final product, a
Custom T-Shirt printed with 2 Colors. This whole process, the loading, printing, and unloading of the shirts, can be accomplished at a reasonably fast rate. Thus you can see why the quantity of shirts is such an important factor in determining a price for
Custom Screen Printing. Once the production run is complete the ink can be scraped out of the screen and back into the bucket, the squeegee cleaned, and the screen is now ready to be reclaimed, returning us to the beginning of the cycle.
Shirt Art, Inc - Custom Screen Printing and Embroidery 2869 PS Business Center Dr.Woodbridge, VA 22912 Phone: 703-680-3963Toll Free: 18003529097 email:
ShirtArt@att.net website:
http://www.shirtartinc.com/Screen Printing:
http://www.shirtartinc.com/screenprintingcustomtshirts.htmEmbroidery:
http://www.shirtartinc.com/customembroidery.htm